The Cornerstone of Modern Manufacturing
What is Injection Moulding?
Injection moulding stands as one of the most versatile and widely used manufacturing processes in the contemporary industrial landscape. From producing intricate components of consumer electronics to crafting durable automotive parts, injection moulding has revolutionised the way we manufacture plastic products.
Injection moulding is a manufacturing process used to produce a vast array of plastic products by injecting molten material into a mould cavity under high pressure. The process allows for the creation of complex shapes with precision and repeatability, making it ideal for mass production.
The Process in Detail:
1. Material Selection: The process begins with the selection of suitable thermoplastic or thermosetting polymers. These materials are chosen based on the desired properties of the final product.
2. Melting: The selected material is then heated until it reaches a molten state. The temperature and viscosity of the molten material are carefully controlled to ensure optimal flow and filling of the mould cavity.
3. Injection: Once the material is molten, it is injected into the mould cavity under high pressure. The pressure helps to fill the entire cavity and ensures that the final product is free of voids or defects.
4. Cooling: After the cavity is filled, the molten material is allowed to cool and solidify inside the mould. Cooling time varies depending on the material and the complexity of the part.
5. Ejection: Once the material has cooled and solidified, the mould opens, and the finished part is ejected from the cavity. In some cases, secondary operations such as trimming or assembly may be required to complete the part.
Key Advantages of Injection Moulding:
1. High Efficiency: Injection moulding enables high-volume production with minimal waste, making it a cost-effective manufacturing solution.
2. Versatility: The process can accommodate a wide range of materials and produce parts with varying complexities, from simple shapes to intricate designs.
3. Precision and Consistency: Injection moulding allows for tight tolerances and precise control over dimensions, ensuring uniformity across multiple parts.
4. Design Flexibility: With the ability to create complex geometries and intricate details, injection moulding offers unparalleled design freedom.
5. Reduced Labour Costs: Automation of the injection moulding process reduces the need for manual labour, further enhancing efficiency and reducing production costs.
Applications Across Industries:
Injection moulding finds applications across a multitude of industries, including automotive, aerospace, medical, electronics, and consumer goods. It is used to manufacture a wide range of products, including plastic components, housings, packaging, and appliances, among others.
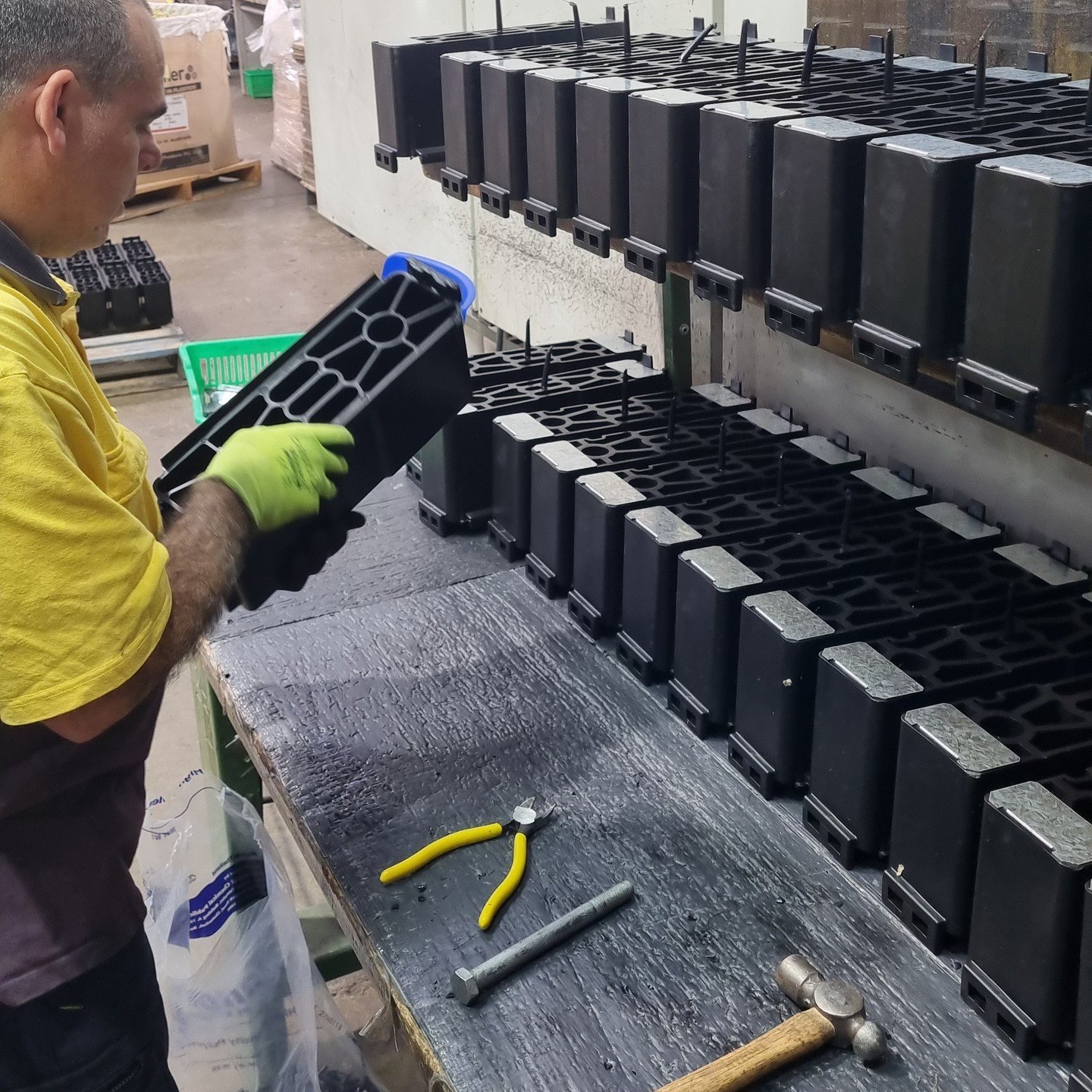
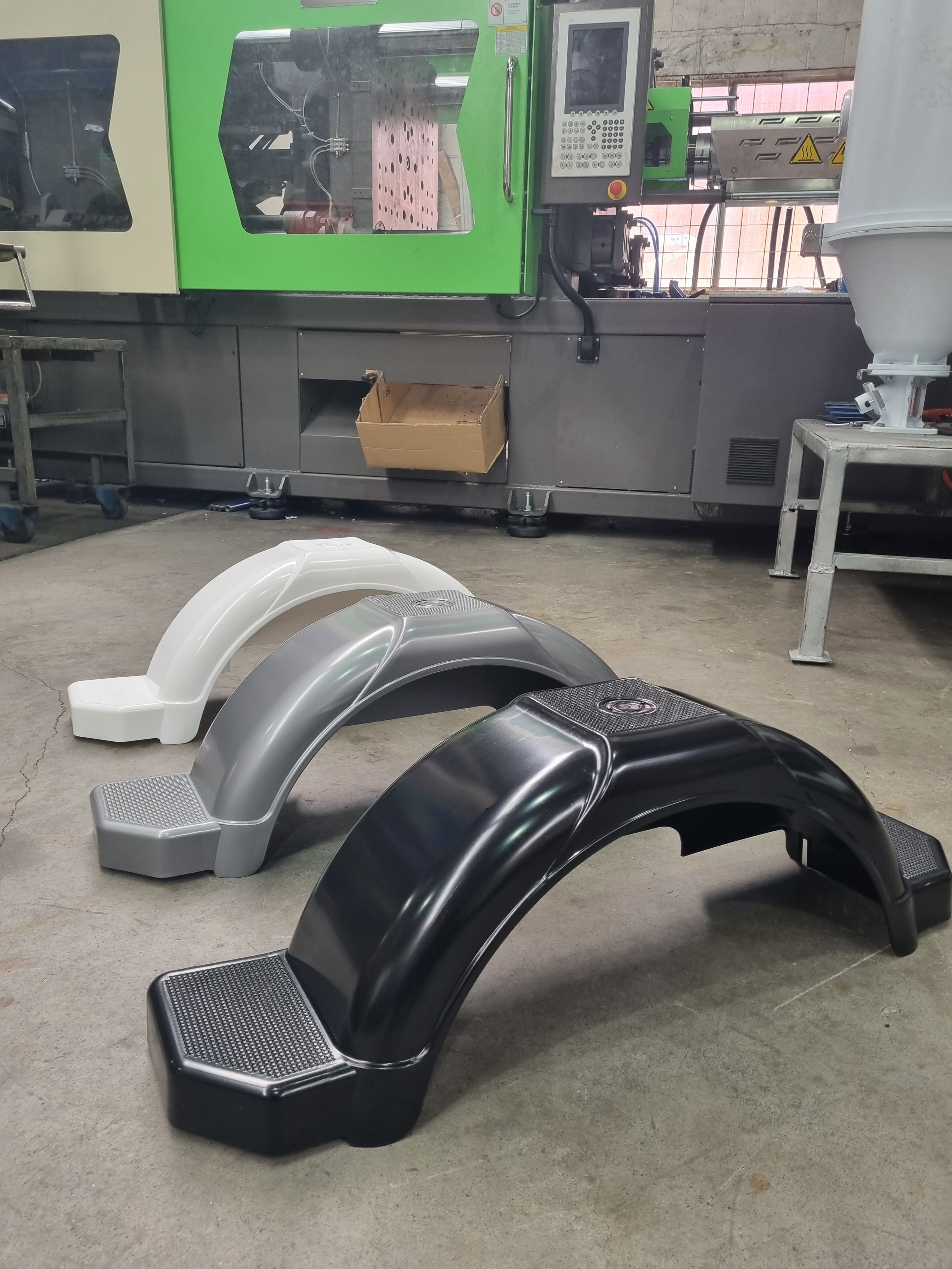
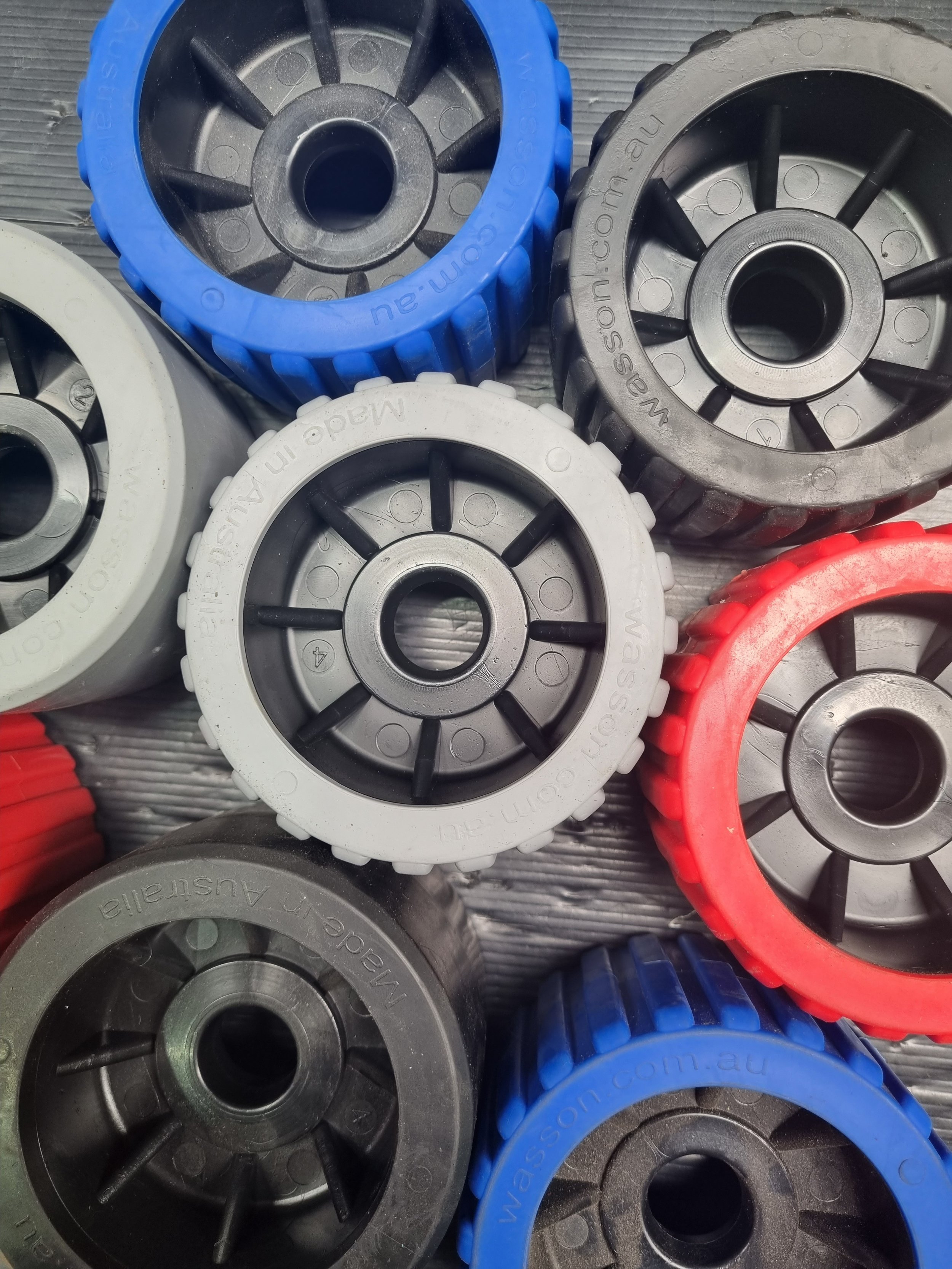
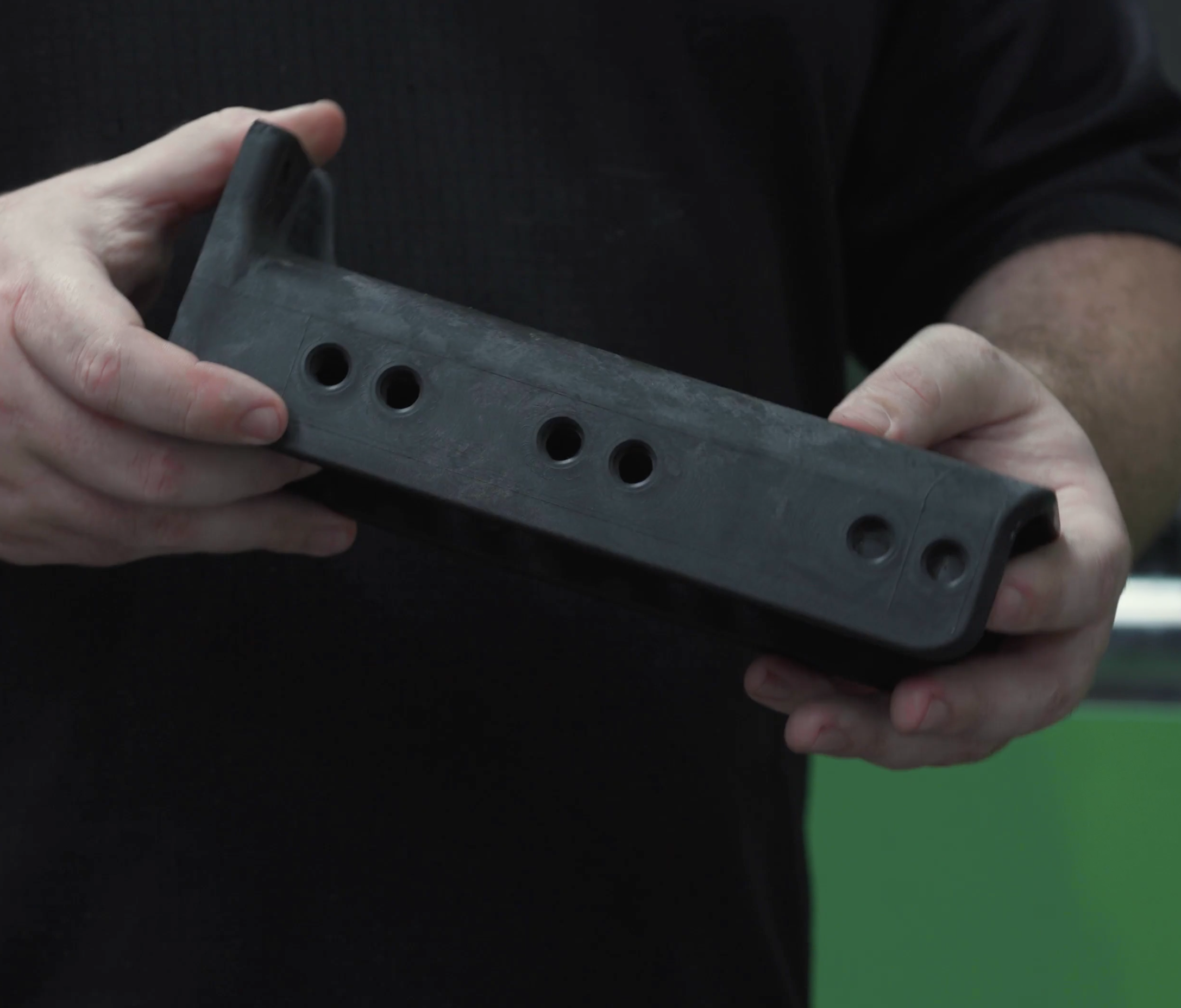

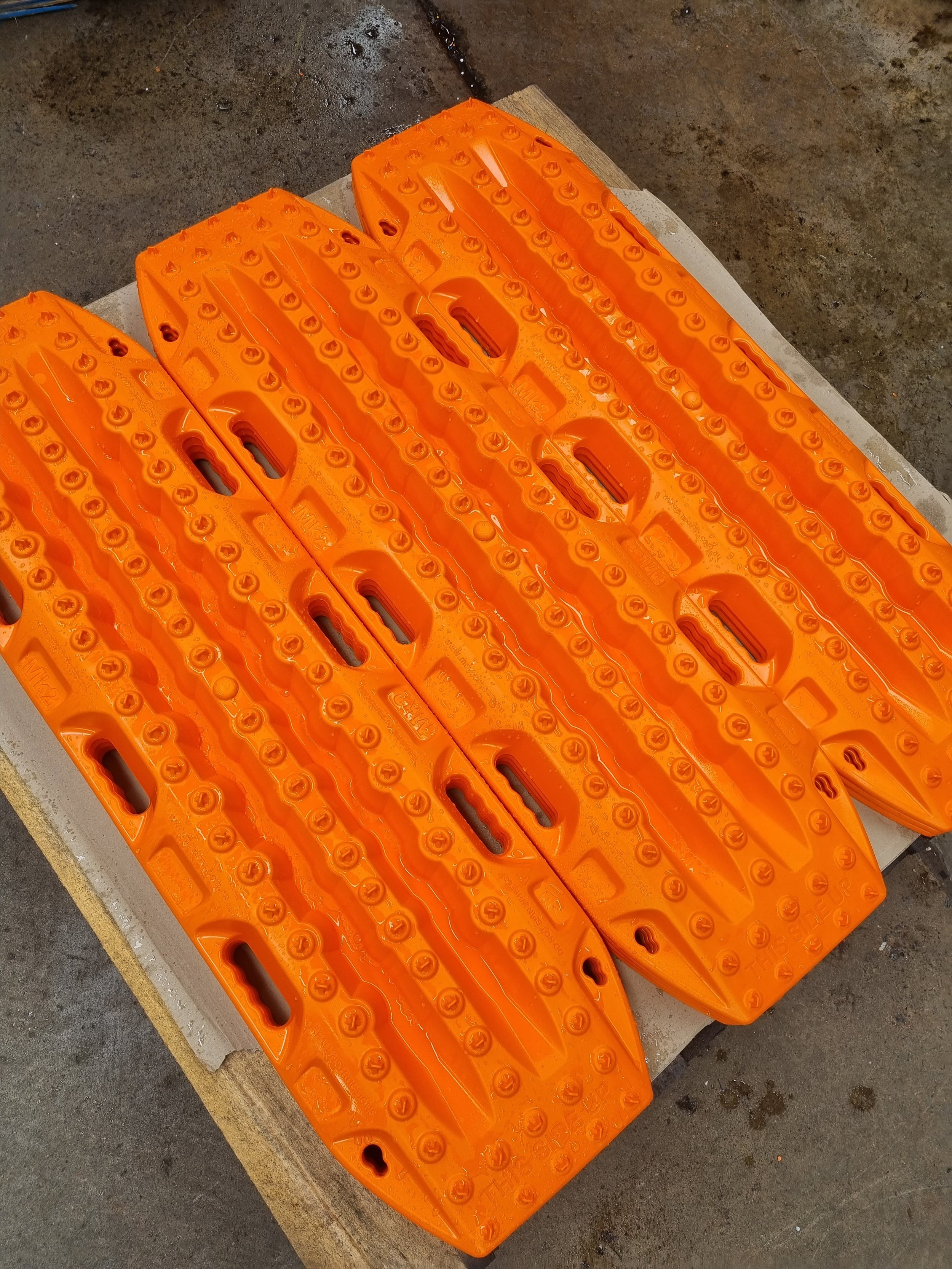
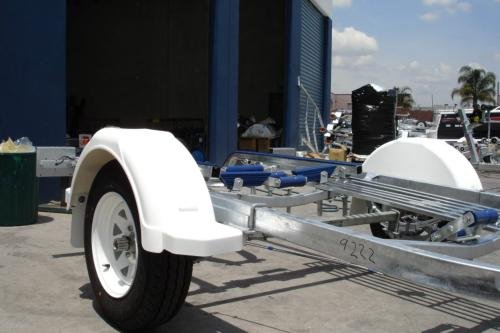

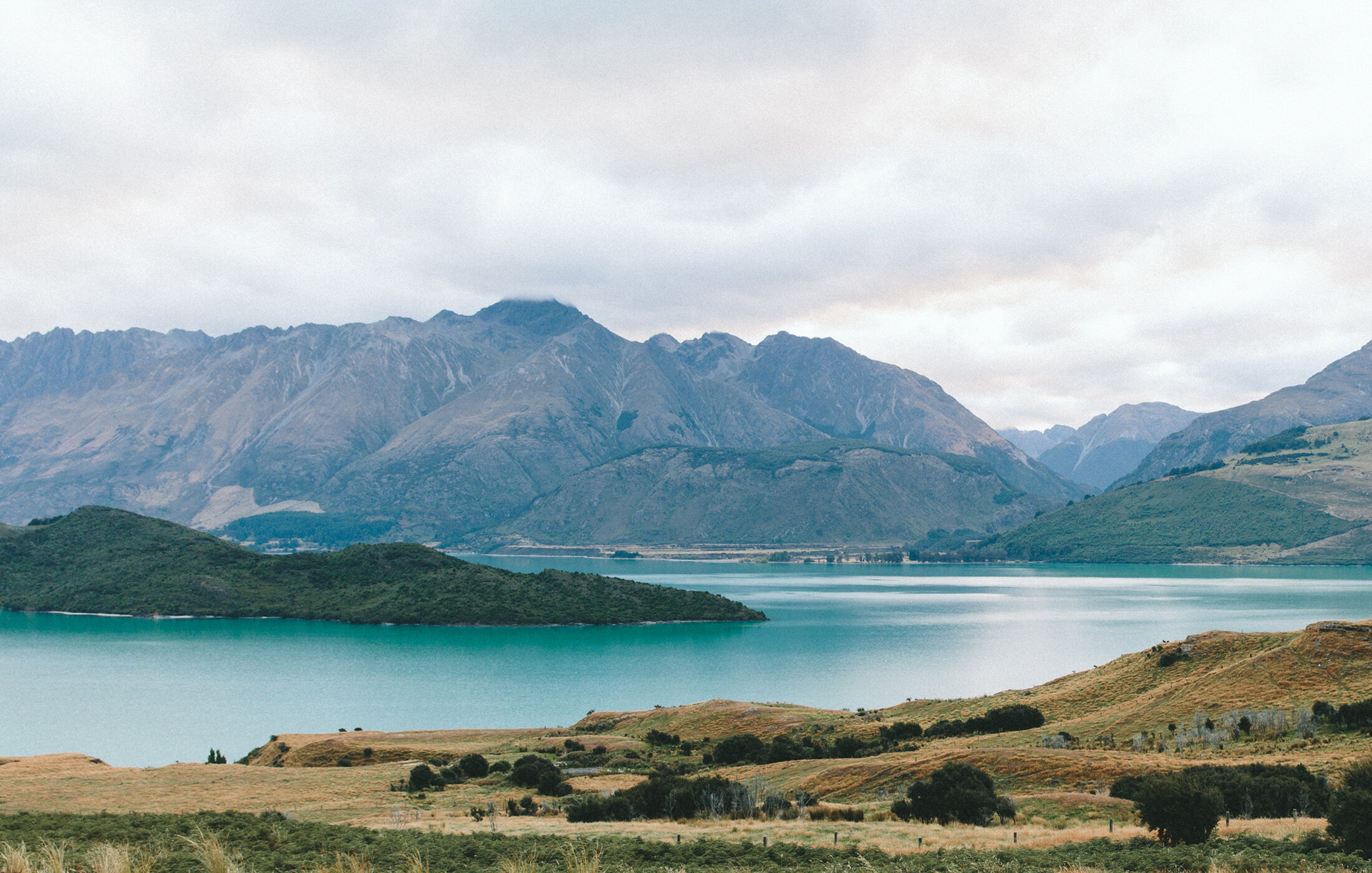